Rutger Werkhoven, Responsable QHSE chez Kooi Group, se réjouit de cette avancée :
" En 2030, nous visons 0 % d’émissions de CO₂. Nous cherchons donc constamment à améliorer notre durabilité : dans notre flotte, nos bâtiments, mais aussi dans nos systèmes. Le plus grand défi était d’innover aussi dans notre choix de matériaux. Avec l’acier Bluemint, nous franchissons aujourd’hui une étape majeure. "
Méthode de fabrication
Pour les nouvelles générations d’UFO, Oreel a commandé plusieurs dizaines de tonnes d’acier Bluemint. Sytse Oreel explique : « Le Bluemint est le même acier, mais produit de manière durable. Thyssen collecte la ferraille et la transforme en acier neuf. Les tôles sont ensuite découpées aux bonnes dimensions puis expédiées chez nous. Nous les transformons alors en structures sur mesure pour les caméras Kooi. L’acier doit être à la fois résistant à la traction et à l’usure. »
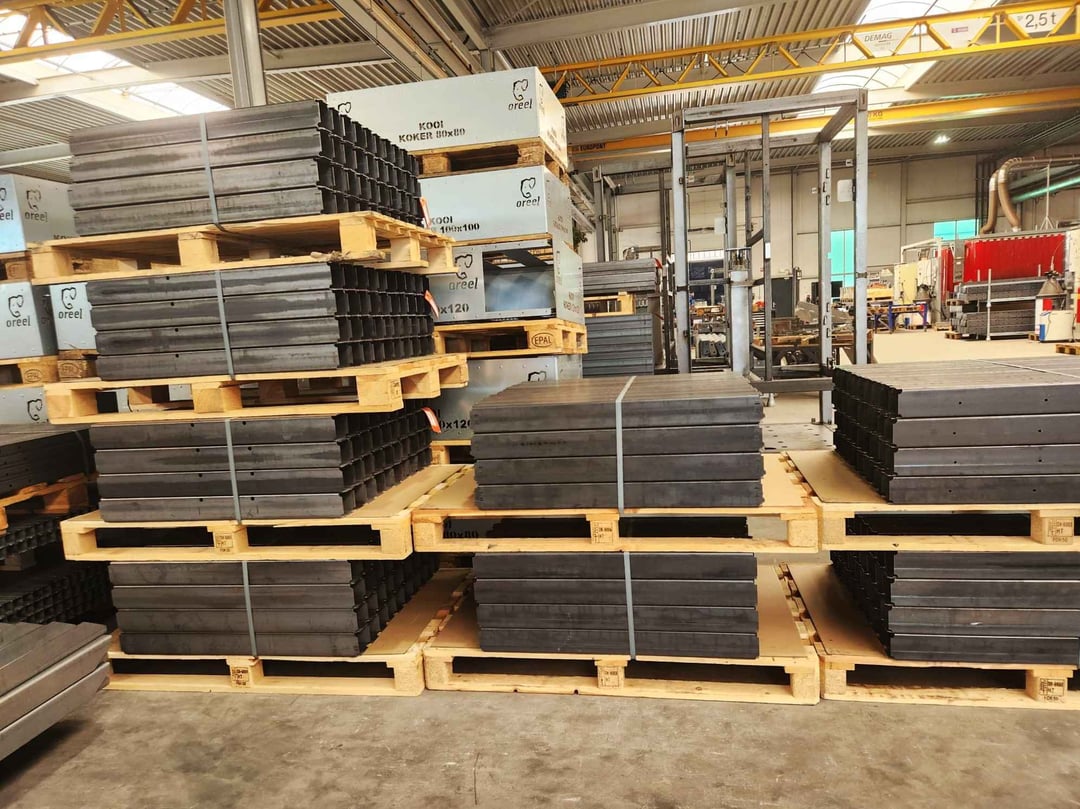
Une collaboration de longue date
Oreel est un fournisseur de Kooi depuis la création de Kooi Camera Surveillance en 2010. Ensemble, ils ont développé la structure idéale pour les caméras mobiles. Si les premières structures étaient soudées à la main, toute la ligne de production Kooi est aujourd’hui robotisée.
Sytse : " La robotisation garantit un processus de production efficace, assurant qualité et maîtrise des coûts — une condition essentielle pour répondre aux exigences élevées de Kooi. "
Des ambitions durables partagées
Kooi et Oreel se rejoignent aussi dans leurs ambitions écologiques. « C’est l’un de nos piliers depuis 170 ans », précise Sytse.
" En 2025, nous comptons 3 000 panneaux solaires qui couvrent 70 % de nos besoins énergétiques, et nous sommes totalement indépendants du gaz. Nous réduisons aussi nos déchets en recyclant les chutes d’acier. "
Une opportunité d’économie carbone
Kooi a déjà réalisé d’importants progrès pour rendre ses produits plus écologiques. L’an dernier, par exemple, la Green Energy Box a été lancée, et le carburant HVO100 a remplacé le diesel dans les générateurs électriques. Une récente analyse du cycle de vie des produits montre que, mis à part l’alimentation en énergie verte, c’est l’extraction des matières premières pour les systèmes de caméras qui génère le plus d’émissions de CO₂.
Rutger : " L’énergie et les matériaux représentent chacun 33 % du total des émissions sur le cycle de vie de nos systèmes. L’acier lourd constitue donc le levier majeur d’économies carbone. Et nous venons de faire un grand pas dans ce sens ! "
Pas de marchandage, mais une ambition partagée
Même si la production de l’UFO Prime coûtera légèrement plus cher à Kooi, cela ne freine pas ses ambitions de croissance durable. « En tant qu’industrie, on veut aller dans une direction précise, et c’est appréciable d’avoir un partenaire avec qui on n’a pas besoin de marchander, mais qui partage cette ambition », explique Sytse. Rutger complète :
" Oreel est un partenaire précieux. Nous voulons grandir ensemble. Kooi a récemment remporté un appel d’offres où nous avons obtenu la note maximale sur le critère de durabilité, en nous engageant à utiliser de l’acier vert. C’est réjouissant de voir que cela se concrétise déjà. "
Un rôle de pionnier
Dans les ateliers d’Oreel à Hallum, la ligne de production dédiée à Kooi est désormais entièrement équipée pour produire les nouvelles structures en acier Bluemint, séparée des autres lignes utilisant l’ancien acier. Les premiers cadres Bluemint pour les UFO Prime viennent tout juste de sortir de production. Une étape qui mérite une photo souvenir.
Sytse : " Pour les PME et le secteur de la mécanique aux Pays-Bas, c’est une nouvelle avancée. Beaucoup se concentrent encore uniquement sur la réduction des coûts, et dans ce contexte, les solutions durables, un peu plus chères, sont moins urgentes. C’est un fait. Heureusement, Kooi aime jouer un rôle de pionnier — et nous aussi. "
Un peu de patience…
En achetant l’acier en plus grande quantité, Sytse espère convaincre d’autres clients, en plus de Kooi, d’opter pour le Bluemint. Mais comme le dit le proverbe, « Tout vient à point à qui sait attendre. » Cela laisse le temps aux deux partenaires de réfléchir à la prochaine étape : produire des structures sans aucune émission de CO₂.